Packaging Machine Repair Service: Making Certain Very Little Downtime and Maximum Performance
Packaging Machine Repair Service: Making Certain Very Little Downtime and Maximum Performance
Blog Article
Understanding the Trick Parts and Repair Service Techniques for Product Packaging Equipment Maintenance
Efficient maintenance of product packaging makers depends upon an extensive understanding of their vital elements, including the framework, drive system, and securing systems. Identifying common maintenance concerns, combined with the execution of preventative methods and fixing techniques, can dramatically boost maker dependability. The selection of repair service methods, consisting of the use of OEM parts and the relevance of certified professionals, plays a critical function in lessening downtime. To truly grasp the complexities of these systems and their upkeep, one need to think about the wider ramifications of disregarding these important practices.
Trick Components of Product Packaging Equipments
Packaging makers are composed of several essential elements that collaborate to guarantee efficient and efficient product packaging processes. At the core of these machines is the structure, which gives structural integrity and houses the various operating parts. The drive system, often a mix of gears and electric motors, facilitates the movement of elements, enabling specific procedure throughout the product packaging cycle.
Another essential component is the conveyor system, which transports items with different stages of the product packaging procedure. This is commonly matched by sensing units and controls that monitor the setting and rate of things, ensuring synchronization and reducing mistakes. The loading system is important for precisely dispensing the right amount of product right into plans, whether in fluid, powder, or strong kind.
Sealing systems, consisting of heat sealants or glue applicators, play an important duty in protecting bundles, protecting against contamination and extending life span. Furthermore, identifying systems are indispensable for providing required item information, making certain conformity with guidelines. The control panel, furnished with user-friendly interfaces, enables operators to manage device features, screen performance, and make modifications as needed, ensuring optimal productivity and performance in packaging procedures.
Usual Upkeep Problems
Effective procedure of product packaging makers depends heavily on normal maintenance to avoid common concerns that can interrupt production. Among these problems, mechanical wear and tear is widespread, specifically in elements like electric motors, conveyors, and seals, which can bring about unforeseen downtimes. In addition, imbalance of parts can lead to inefficient procedure, causing products to be improperly packaged or harmed during the procedure.
Another common maintenance issue involves the accumulation of dust and particles, which can disrupt the maker's sensing units and relocating components. packaging machine repair service. This not just impacts efficiency but can likewise pose safety threats. Lubrication failures can lead to boosted rubbing, resulting in overheating and ultimate part failing.
Electrical issues, typically originating from loose links or worn-out wiring, can interrupt machinery functions, leading to considerable manufacturing hold-ups. Finally, software glitches as a result of obsolete programs or improper setups can impede the equipment's operation, demanding immediate intervention. Attending to these common upkeep problems proactively is important for guaranteeing optimum efficiency and long life of product packaging equipment.
Preventative Maintenance Strategies
Carrying out preventative upkeep approaches is crucial for sustaining the effectiveness and dependability of packaging equipments. These techniques incorporate an organized strategy to upkeep, concentrating on the regular examination and maintenance of equipment to preempt potential failings. By sticking to a scheduled maintenance program, drivers can identify damage on elements prior to they result in considerable break downs.
Crucial element of a preventative upkeep technique consist of routine inspections, cleansing, component, and lubrication substitutes based upon manufacturer suggestions. Utilizing checklists can enhance this procedure, making certain that no vital jobs are neglected. In addition, keeping exact documents of upkeep tasks help in tracking the maker's efficiency with time, facilitating informed decision-making concerning future maintenance demands.
Training staff on the relevance of preventative upkeep boosts compliance and fosters a culture of proactive treatment. Implementing an anticipating upkeep part, making use of information analytics and sensor innovation, can even more optimize machinery efficiency by forecasting failings before they happen.
Repairing Strategies
When faced with malfunctions or inefficiencies in product packaging equipments, using organized troubleshooting methods is vital for identifying and fixing problems promptly. The initial step in effective troubleshooting is to develop a clear understanding of the machine's functional parameters and efficiency metrics. This includes reviewing the maker's specifications, along with any mistake alerts or codes shown.
Next, drivers should perform a visual examination, looking for obvious indications of damages, misalignment, or wear. This commonly includes examining belts, sensors, and gears to pinpoint prospective sources of malfunction. Gathering functional information, such as production rates and downtime why not check here logs, can likewise provide insights into reoccuring issues.
Once prospective troubles are identified, using a rational strategy to separate the origin is essential. This my link may need testing private components or systems in a controlled manner. Participating in conversations with drivers that connect with the equipment frequently can produce beneficial responses concerning uncommon actions or patterns.
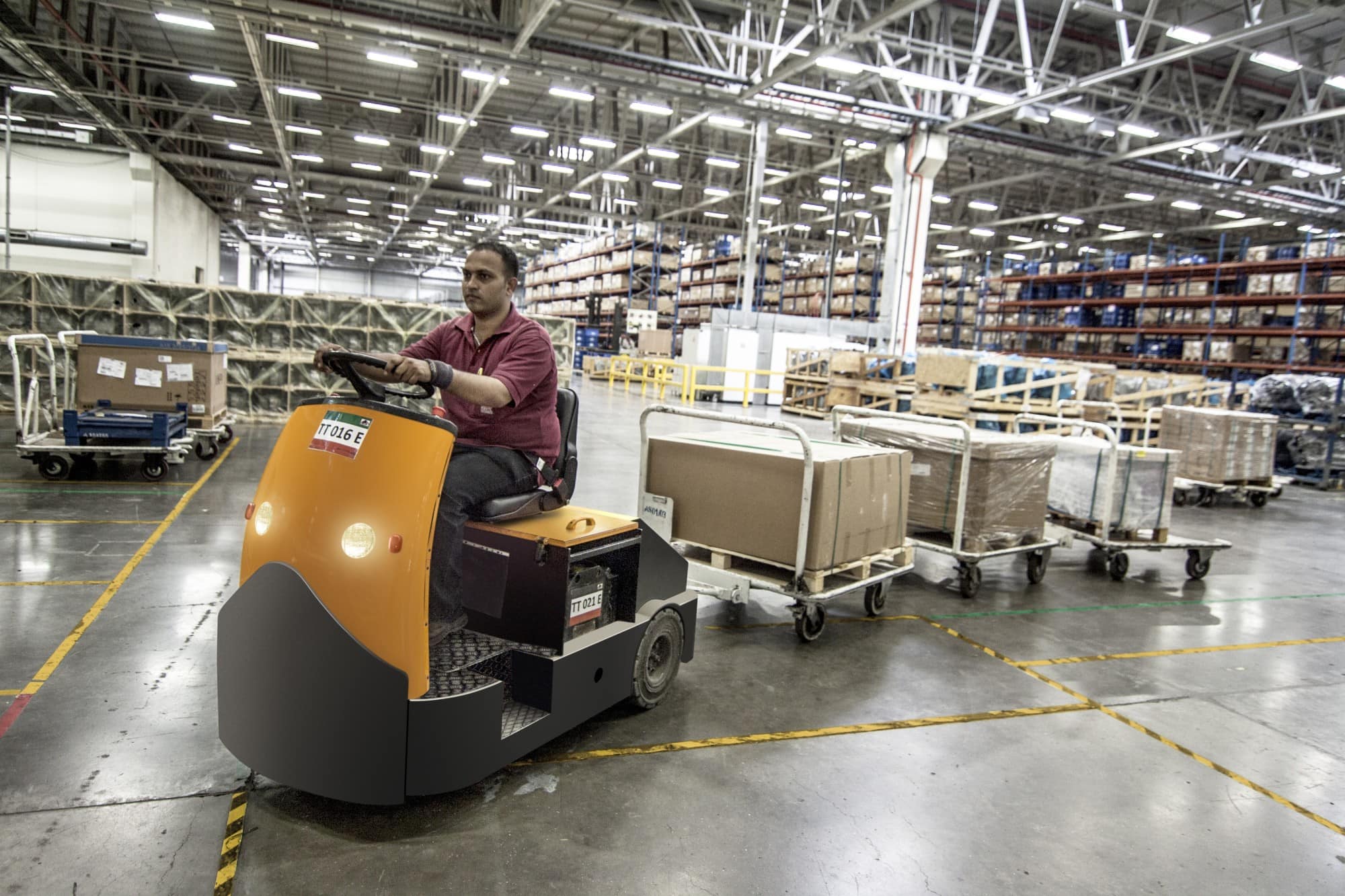
Fixing and Substitute Best Practices
A comprehensive understanding of repair and substitute finest practices is vital for maintaining the long life and performance of product packaging makers. On a regular basis evaluating the condition of equipment elements permits for timely intervention, avoiding even more substantial problems that can bring about expensive downtimes.
When repairs are needed, it is vital to utilize OEM (Original Devices Supplier) parts to make certain compatibility and performance. This not just preserves the stability of the machine however additionally supports service warranty contracts. In addition, it is recommended to keep an inventory of important spare parts to promote quick substitutes and decrease operational disturbances.
For complex repair services, engaging licensed technicians with specialized training in packaging equipment is advised. They possess the know-how to detect issues precisely and implement repair work effectively. In addition, documenting all repair work activities and components substitutes is essential for preserving a thorough maintenance history, which can help in future troubleshooting.
Lastly, implementing a proactive method, including routine assessments and anticipating maintenance methods, improves the integrity of product packaging devices. By sticking to these ideal techniques, organizations can make certain optimum equipment efficiency, minimize operational risks, and extend tools life-span.
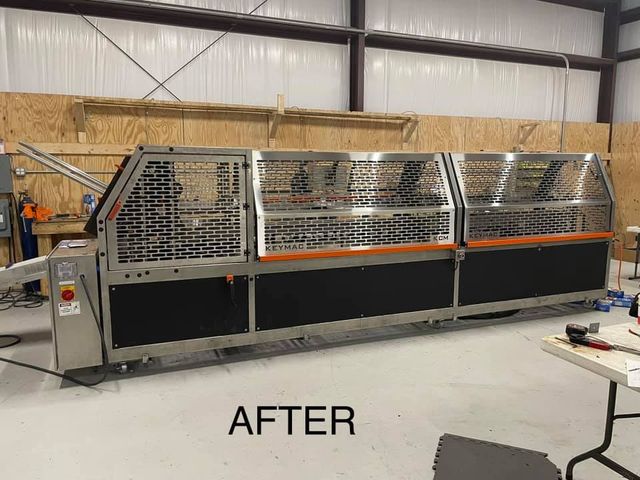
Final Thought
In conclusion, a complete understanding of product packaging machine components and efficient upkeep methods is essential for optimal performance. By executing these methods, companies can make sure the long life and efficiency of packaging devices, eventually adding to boosted operational efficiency and minimized prices (packaging machine repair service).
Reliable upkeep of product packaging equipments pivots on a complete understanding of their vital parts, consisting of the frame, drive system, and sealing mechanisms.Efficient procedure of packaging devices depends greatly on normal upkeep to prevent common problems that can interfere with manufacturing.Applying preventative upkeep strategies is essential for sustaining the efficiency and reliability of packaging makers. In addition, maintaining precise imp source records of maintenance tasks help in tracking the maker's efficiency over time, helping with notified decision-making concerning future upkeep demands.
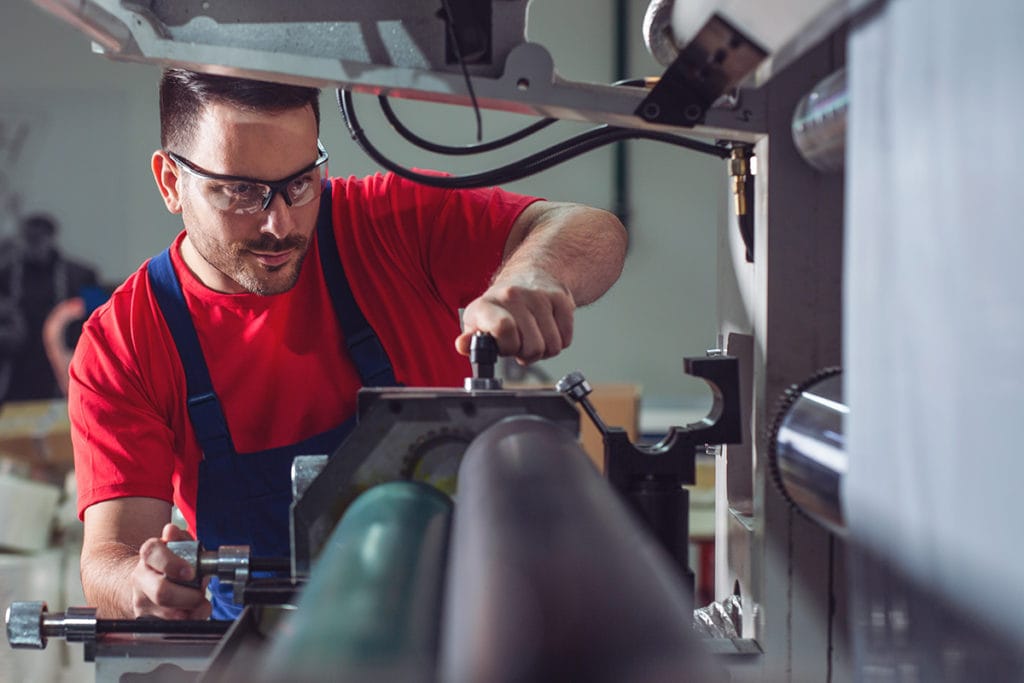
Report this page